Обучение специалистов акустико-эмиссионному контролю
Оценка технического состояния сильфонных трубопроводных компенсаторов без вывода из эксплуатации //Научно-технический журнал «Нефтегазовое дело», т.12 №1 2014г.
Оценка технического состояния сильфонных трубопроводных компенсаторов без вывода из эксплуатации
Давыдова Д.Г.1, Кузьмин А.Н.1, Гроховский В.И.2, Ризванов Р.Г.3, Аксельрод Е.Г.1, Абдрахманов Н.Х.4
1 ООО «Стратегия НК», г. Екатеринбург, Российская Федерация
2 ФГАОУ ВПО «Уральский федеральный университет имени первого Президента России Б.Н.Ельцина», г. Екатеринбург, Российская Федерация
3 ФГБОУ ВПО «Уфимский государственный нефтяной технический университет», г.Уфа, Российская Федерация
4 Ассоциация «Башкирская Ассоциация экспертов», г. Уфа, Российская Федерация
//Научно-технический журнал «Нефтегазовое дело», т.12 №1 2014г.
В статье приведены результаты акустико-эмиссионного контроля промышленного оборудования без вывода из эксплуатации. Предложен метод идентификации нестационарных шумов, основанный на беспороговой регистрации данных и расчете локальных статистических параметров акустико-эмиссионного сигнала и шума. Для оценки технического состояния компенсаторов без вывода их из эксплуатации впервые был использован подход, предполагающий одновременное использование двух независимых систем регистрации акустико-эмиссионного сигнала: стандартной системы и установки беспороговой регистрации данных. Принципиальное отличие системы беспороговой регистрации данных заключается в отказе от использования метода амплитудной пороговой дискриминации. Ключевой особенностью обработки акустико-эмиссионных данных является использование подвижного временного окна.
Показано, что совместное использование стандартной акустико-эмиссионной системы с порогом дискриминации (по амплитуде входного сигнала) и устройства беспороговой регистрации данных позволяет исключить ложные локации, возникающие в условиях интенсивных нестационарных помех. Показано, что использование беспороговой регистрации данных позволяет сохранить форму акустико-эмиссионного сигнала, что исключает вероятность информационных потерь при обработке данных. Расчет статистических характеристик в скользящем временном окне надежно фиксирует наличие источников акустической эмиссии, не связанных с фоновым шумом. Сравнительный анализ сигналов, зарегистрированных при контроле нескольких единиц оборудования, позволяет выявлять нестационарные помехи. Проиллюстрированы возможности металлографических исследований и электронно-зондового микроанализа при диагностировании межкристаллитной коррозии. Показано, что непрерывные локации, возникающие при акустико-эмиссионном контроле, вызваны разрушением металла под воздействием межкристаллитной коррозии с образованием карбидов хрома по границам зерен.
Ключевые слова: акустико-эмиссионной контроль, беспороговая регистрация данных, металлографические исследования.
В настоящее время чрезвычайно востребовано техническое диагностирование оборудования без вывода из эксплуатации. При таком подходе существенно снижаются экономические затраты, связанные с необходимостью изменения рабочего цикла, а некоторых случаях с полной остановкой производства. С другой стороны, в этом случае проведение контроля не зависит от сроков плановых ремонтов и позволяет получать оперативные данные о техническом состоянии объекта в реальном времени. В связи с этим активно развиваются методы оценки состояния в режиме мониторинга. Такие возможности, в частности, открывает акустико-эмиссионный (АЭ) контроль.
В статье приведен подход технического диагностирования действующего промышленного оборудования. Объектом контроля выступали осевые сильфонные компенсаторы, установленные на трубопроводе перегретого пара. Конструкция компенсатора этого типа представляет собой гибкий металлорукав из гофрированной оболочки, расположенной между скрепленными с трубопроводом концевыми патрубками. Диаметр компенсатора – 830мм, материал – INCOLOY 800H, среда – перегретый водяной пар. Эксплуатационные параметры: давление 0,1 МПа, температура 800°С. Рассматриваемые компенсаторы расположены в пределах одного участка трубопровода. К основным дефектам компенсаторов относятся: коррозионные дефекты; усталостные трещины, возникающие вследствие неоднородного распределения нагрузки; пережог металла внутренней стенки при наличии солевых отложений; дефекты отливки и термообработки; усталостные разрушения на участках, подверженных повышенной вибрации.
Необходимость внеочередного технического диагностирования была вызвана рядом инцидентов, связанных с аварийными ситуациями вследствие разрушения оборудования. Проведение контроля существенно осложнялось тем фактом, что рассматриваемые компенсаторы установлены на действующей производственной линии, остановка которой возможна в ограниченный период времени при наличии резервирующих устройств. Кроме того при проведении АЭ контроля термокомпенсирующих элементов трубопровода без изменения рабочего цикла работы присутствует большое число нестационарных шумов различной природы: пневматический и гидродинамический шум движения рабочей среды в объекте контроля, структурный шум (релаксационные процессы при локальных термомеханических возмущениях), высокоамплитудные импульсные электрические помехи, внешние механические и электромагнитные помехи, конструктивный шум (процессы трения при взаимном перемещении поверхностей скольжения металла в слоях гофры), релаксационные шумы после восстановительных или ремонтных работ.
Поскольку существующие системы АЭ контроля обладают низким уровнем помехозащищенности к такого рода шумам [1], а возможность проведения необходимого комплекса работ по снижению уровня шумов [2] отсутствует, высока вероятность появления ложных локаций АЭ сигнала, что в свою очередь влечет неверную трактовку результатов контроля.
Стоит отметить, что температура транспортируемого продукта составляла 800°С, температура поверхности компенсаторов и трубопроводов – не менее 600°С. Очевидно, что использование стандартных методов неразрушающего контроля (ультразвуковой контроль и толщинометрия, капиллярная и магнитопорошковая дефектоскопия, вихретоковый контроль и т.д.) в данном случае невозможно. Кроме того, применяемые в современной практике методы неразрушающего контроля зачастую носят локальный характер и не дают возможности оценить общее состояние технического устройства. Подход, используемый в настоящее время для оценки технического состояния, основан на обследовании наиболее нагруженных узлов и элементов, работающих в наиболее неблагоприятных условиях; при этом места контроля носят унифицированный и «стандартизованный» характер. Напротив, применение АЭ контроля позволяет получать интегральную оценку текущего состояния оборудования, не требуя снятия значительных объемов изоляции. Проблема высокой температуры в рамках данной работы была решена с использованием волноводов и их дополнительной теплоизоляции, таким образом, чтобы температура на рабочей площадке находилась в пределах допуска для использования стандартных АЭ преобразователей.
Учитывая вышесказанное, было принято решение о проведении технического диагностирования, включающего акустико-эмиссионный контроль и вибрационную диагностику. Дополнительно для проведения металлографического исследования и электронно-зондового микроанализа были подготовлены образцы металла компенсаторов, выведенных из эксплуатации.
Для оценки технического состояния компенсаторов без вывода их из эксплуатации впервые был использован подход, предполагающий одновременное использование двух независимых систем регистрации АЭ сигнала: стандартной АЭ системы (с выбором величины порога амплитудной дискриминации) A-Line32D и установки беспороговой регистрации данных (БРД).
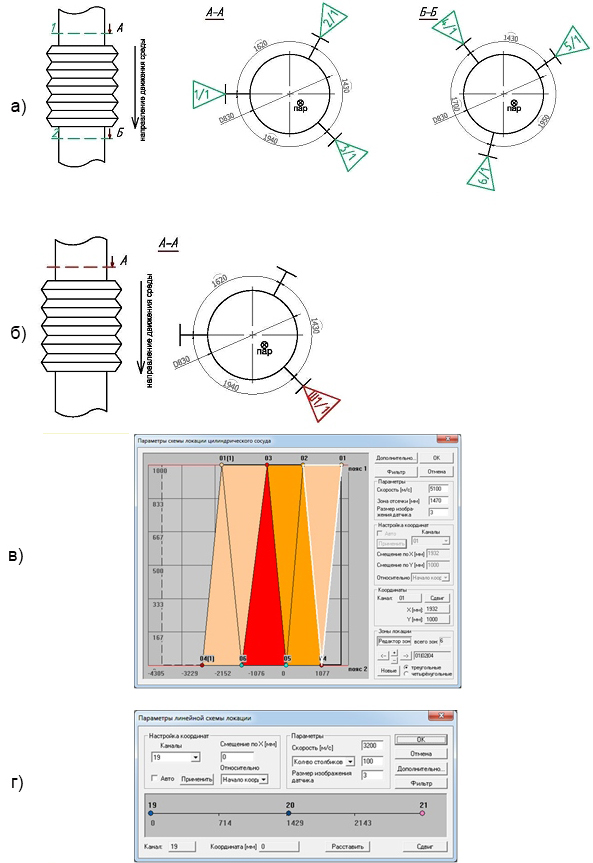
В ходе акустико-эмиссионного контроля с применением стандартной АЭ аппаратуры были выявлены компенсаторы с источниками АЭ. Временные зависимости пиковых амплитуд АЭ сигналов, превышающих порог дискриминации, представлены на рисунках 2а и 3а. При использовании амплитудно-динамического и интегрального критериев [2] было установлено, что обнаруженные источники АЭ соответствуют II (компенсатор №1, рисунок 2а) и III (компенсатор №3, рисунок 3а) классу опасности, что свидетельствует о наличии опасных развивающихся дефектов. Обнаруженные при этом лоцируемые АЭ сигналы имеют высокоамплитудный, дискретный характер, соответствующий поведению опасного развивающегося дефекта. Установлено, что шумовая случайная компонента имеет неоднородный по каналам характер и, тем самым, вносит существенный вклад в регистрируемые параметры. При этом для АЭ сигнала, имеющего источники АЭ IIIкласса опасности, обнаруженные локации устойчиво проявлялись на протяжении всей записи параметров АЭ как для плоскостной, так и для линейной локации.
Рисунок 2. Результаты АЭ контроля компенсаторов №1 и №2.
Для сравнения на рисунках 2б и 3б приведены соответствующие амплитудно-динамические параметры и локационная диаграмма, полученные при контроле бездефектных компенсаторов (компенсаторы №2 и №4).
Рисунок 3. Результаты АЭ контроля компенсаторов №3 и №4.
Принципиальное отличие системы беспороговой регистрации данных заключается в отказе от использования метода амплитудной пороговой дискриминации [5]. Устройство БРД была специально спроектировано для измерения и анализа АЭ сигнала на базе серийного модуля преобразователя напряжений L-Card Е20-10D (производство ООО «Л-КАРД», г. Москва). Для реализации АЭ контроля с использованием БРД на каждый компенсатор был установлен один датчик (рисунок 1б), расположенный в непосредственной близости от датчиков A-Line 32D. Диагностическая информация, поступающая с объекта контроля, представляет собой временной ряд, состоящий из аддитивной смеси сигнала от дефекта и шума. Регистрация сигнала АЭ велась в широкой полосе частот фильтра 30÷500 кГц посредством датчика LD-11 и широкополосного предусилителя. Калибровка схемы измерения осуществлялась с использованием имитатора «полезного» сигнала (источник Су-Нильсена) и шума (генератор шума). С преобразователя АЭ сигнал поступал на высокоскоростную четырехканальную плату АЦП с частотой оцифровки сигнала на входе 2,5 МГц на канал. Далее сигнал в цифровом виде вводился в блок обработки данных, реализованного на основе программного комплекса MATLAB. Ключевой особенностью обработки АЭ данных БРД является использование подвижного временного окна, другими словами, расчетные операции выполняются внутри выбранного временного интервала, «скользящего» по временному ряду АЭ сигнала. Ширина временного окна составляла 0,2мс÷4мс. Его величина определялась таким образом, чтобы внутри временного окна сигнал оставался квазистационарным, а также была возможность оценить динамику изменения вычисляемых параметров.
Основным диагностическим признаком является текущее значение статистических характеристик случайного акустического шума в момент возникновения и развития источников АЭ. При возникновении источников АЭ сигнала, связанных с развитием дефектов в объекте контроля (развивающаяся трещина, коррозионные процессы), природа регистрируемого акустического шума существенно изменяется [3], а соответствующие статистические характеристики принимают нешумовой детерминированный характер. В данной работе при обработке данных, полученных при беспороговой регистрации, вычислялись значения следующих статистических параметров временного ряда АЭ [6]: дисперсия, среднее квадратичное значение, асимметрия, эксцесс. Результатом обработки являются временные ряды, состоящие из локальных статистических параметров. Стоит отметить, что в условиях БРД анализируются не интегральные характеристики АЭ сигнала, превышающего порог (амплитуда, энергия, длительность сигнала, интенсивность) [4], а локальные (мгновенные) статистические параметры. Соответственно, отношение сигнал/шум, в отличие от систем пороговой регистрации, может быть в этом случае порядка или меньше единицы. Последнее условие для систем диагностического мониторинга является фактором, определяющим эффективность применения БРД.
В каждой серии замеров принимали участие два компенсатора. Существенно, что расстояние между датчиками выбиралось таким образом, чтобы исключить вероятность попадания АЭ сигнала от дефекта на оба измерительных канала. При этом совпадение резких изменений локальных статистических характеристик на временных шкалах, относящихся к различным датчикам, дает основание полагать, что в этот момент времени возникает помеха, не связанная с наличием дефекта. Таким образом реализуется схема АЭ контроля, которая позволяет выявлять помехи, вызывающие ложное срабатывание стандартной пороговой АЭ системы.
На рисунках 2в, 2г, 3в приведены статистические параметры АЭ сигналов при контроле компенсаторов с применением БРД. Для наглядности рассмотрены как компенсаторы, которые по результатам контроля с применением АЭ системы A-Line признаны бездефектными (компенсаторы №2 и №4), так и компенсаторы, имеющие источники АЭ (компенсаторы №1 и №3). Практическая значимость анализа рисунков 2в, 2г, 3в заключается в том, что появляется возможность выявить наличие нестационарной высокоамплитудной помехи, «подстраивающейся» под вид «полезного» сигнала АЭ. Так на рисунках 2в и 2г отклонения статистических характеристик от фонового шума оказались идентичными, что свидетельствует о наличии высокоамплитудной помехи, приходящей на оба измерительных канала одновременно. Это позволило сделать вывод о бездефектной природе зарегистрированных в ходе АЭ контроля источников АЭ II класса опасности (компенсатор №1). Косвенно этот факт был подтвержден в ходе повторного контроля данного компенсатора, где источники АЭ не были выявлены.
Как видно на рисунке 3в (компенсатор №3) присутствуют ярко выраженные дополнительные максимумы отклонений от шума, отсутствующие при контроле компенсатора №4. Последнее подтвердило результаты контроля с применением АЭ системы A-Line о дефектной природе компенсатора №3.
При сравнении результатов АЭ контроля с применением пороговой системы регистрации данных и БРД, установлено, что на рисунке 3а присутствуют многочисленные импульсы (в диапазонах 150÷170 и 500÷600 секунд), аналоги которых отсутствуют на рисунке 3в. В ходе постобработки данных БРД с применением адаптивной фильтрации было подтверждено наличие импульсов АЭ в рассматриваемых интервалах. Подробное описание подхода обработки данных АЭ контроля с применением адаптивной фильтрации является предметом отдельной публикации.
Оценка уровня вибрации производилась путем измерения виброскорости (среднее квадратичное значение), виброускорения (пиковое значение) и виброперемещений (размах параметра) в контрольных точках трубопровода. Участки контроля были назначены в местах наибольшей вибрации в вертикальном, горизонтальном и осевом направлениях. Обнаружено, что текущие значения вибрации идентичны для всех компенсаторов, а по абсолютной величине соответствуют минимальным начальным уровням вибрации, не оказывающим существенного влияния на целостность объекта контроля. Таким образом, установлено, что результаты вибрационной диагностики не могут быть использованы для оценки текущего состояния компенсаторов.
Для исследования макро- и микроструктуры металла были подготовлены образцы из внутреннего и наружного слоев гофры компенсатора – образцы № 1 и 2 соответственно (рисунок 4а). Результаты, полученные при металлографическом исследовании материала компенсатора, представлены на рисунке 4. На рисунках 4б, 4в видна характерная структура окисления вдоль границ зерен, при этом нарушается механическая связь между соседними зернами. Такая картина имеет место механизм межкристаллитной коррозии коррозионностойких сталей [7]. При такой разновидности коррозии вдоль границ зерен выделяются фазы, обогащенные хромом, главным образом, карбиды на основе хрома (Cr23C6). Эти карбиды концентрируются на границах зерен, иногда образуя сплошную цепочку. При этом участки, непосредственно окружающие карбиды Cr23C6, оказываются существенно обедненными по хрому (ниже 12%) и становятся электрохимически активными. Характерно, что в данном случае межкристаллитной коррозии подвержен как внутренний слой гофры осевого компенсатора, непосредственно соприкасающийся с транспортируемой средой, так и наружный слой гофры, доступ рабочей среды к которому исключен.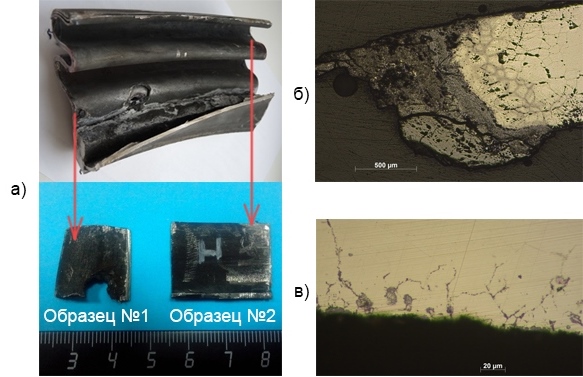
Рисунок 4. Металлографическое исследование металла гофры трубопроводного компенсатора.
На подготовленных образцах дополнительно был проведен электронно-зондовый микроанализ. Микроанализ выполнен с использованием сканирующего электронного микроскопа FE-SEM Zeiss ∑igma VP. В ходе исследования получена информация о локальном химическом составе межзеренных пространств в материале компенсатора. Результаты электронно-зондового микроанализа приведены на рисунке 5. Распределение хрома (рисунок 5д) позволяет сделать предположение о выделении карбидов хрома по границам зерен и обеднению обезлегировании по хрому приграничных областей. Эти процессы характерны для межкристаллитной коррозии. Высокое содержание кислорода в межзеренном пространстве (рисунок 5б) свидетельствует о наличии прокорродировавшей зоны вдоль границ зерен металла (оксиды металлов). Таким образом, электронно-зондовый микроанализ подтвердил ранее высказанное предположение о том, что основным механизмом разрушения материала компенсатора является межкристаллитная коррозия. Кроме того, межкристаллитная коррозия объясняет как непрерывный характер локаций при контроле с применением пороговой АЭ системы, так и постоянные колебания локальных статистических характеристик при анализе результатов БРД.
Рисунок 5. Структура металла и распределение химических элементов в материале гофры компенсатора, образец №1. а) структура металла компенсатора (внутренний слой), б) содержание кислорода, в) содержание железа, г) содержание марганца, д) содержание хрома, е) содержание никеля, ж) содержание титана.
Результаты и выводы
- Предложен метод, позволяющий проводить АЭ контроль действующего оборудования. Показано, что традиционный метод акустико-эмиссионного контроля, а также метод, основанный на беспороговой регистрации, являются взаимодополняющими и могут применяться одновременно, что позволяет исключить ложные локации, возникающие при работе стандартной пороговой АЭ системы в условиях интенсивных нестационарных помех.
- Использование БРД позволяет сохранить форму АЭ сигнала, что исключает вероятность информационных потерь при обработке данных.
- Расчет статистических характеристик в скользящем временном окне надежно фиксирует наличие источников АЭ, не связанных с фоновым шумом. Сравнительный анализ сигналов, зарегистрированных при контроле нескольких единиц оборудования, позволяет выявлять нестационарные помехи.
- Непрерывные локации, возникающие при АЭ контроле и не связанные с помехами, вызваны разрушением металла под воздействием хрома по границам зерен.
Список используемых источников
- Баранов В.М., Гриценко А.И., Карасевич А.М. Акустическая диагностика и контроль на предприятиях топливно-энергетического комплекса. М: Наука, 1998. 304 с.
- ПБ 03-593-03. Правила организации и проведения акустико-эмиссионного контроля сосудов, аппаратов, котлов и технологических трубопроводов. СПб.: Издательство ДЕАН, 2004. 64с.
- Юдин А.А., Иванов В.И. Стохастическая теория акустической эмиссии при пластической деформации. Сообщение 1. Мощность и энергетический спектр сигнала А3 // Диагностика и прогнозирование разрушения сварных конструкций, 1987. №5. С.24-29.
- ГОСТ Р ИСО 12716-2009. Контроль неразрушающий. Акустическая эмиссия. Словарь. М: Стандартинформ, 2011. 12с.
- Аксельрод Е.Г., Давыдова Д.Г., Кузьмин А.Н. Помехоустойчивый метод обнаружения полезного сигнала в системах акустико-эмиссионного мониторинга опасных производственных объектов // Технадзор, 2013. №5(78). С. 86-89.
- Lokajiþek T., Klima K. Sign and arrival time determination of acoustic emission signals by means of high-order statistic approach // Materials of international conference Defectoscopy 2008 Brno, 2008. P.123-129.
- Колотыркин Я.М., Княжева В.М. Итоги науки и техники. Сборник. Серия Коррозия и защита от коррозии. М.: ВИНИТИ, 1974. т. 3. С. 5-83.
ЧИТАЙТЕ ТАКЖЕ:
Совершенствование методики диагностики трубопроводов с применением метода акустической эмиссии